Ryan Wirick
(MBA, PMP, Lean Six Sigma Greenbelt, Agile, Google Certified PM)
Hello! My name is Ryan and it is great to meet you!
This page is my personal bio, including everything from my professional portfolio to my hobbies and personal interests.
Professional Experience
With over 10 years of experience in the life sciences and biotech sectors, I have successfully led projects and teams, driving innovation and excellence. My work includes launching new products, managing business systems portfolios, and building cutting-edge cGMP manufacturing facilities. For a detailed look at my responsibilities and achievements, feel free to check out my LinkedIn profile — let's connect there!
-
As the PMO Manager and Sr PM, I lead the Corporate Program Management team, steering high-impact projects that align with our company’s vision. I excel in crafting effective program strategies from start to finish, ensuring optimal use of resources, and successful project outcomes. My portfolio includes managing high-profile corporate projects, business systems implementations, and overseeing IVD and non-product software development in compliance with ISO and FDA regulations. I'm skilled in meticulous planning and risk management, proactively tackling challenges, and fostering a collaborative work environment. My projects primarily support the Quality, Finance, IT, and Operations teams, covering ERP implementation, Quality Compliance Gap Analysis, Facility Validation, and New Product Development. I take pride in my ability to manage multiple projects remotely, thanks to strong personal time management skills.
-
As the lead founding partner, I provided visionary leadership and executed the establishment of our LLC. As the General Manager, I ensured full compliance with CLIA regulations, achieving certification and maintaining high-quality standards. I built a talented interdisciplinary team, fostering a culture of excellence and collaboration. I also formed a partnership with Yale, integrating our processes into their Saliva Direct program. Additionally, I managed budgeting, financial planning, and resource allocation to ensure our laboratory’s financial health. My consulting projects included COVID-19 campus surveillance testing programs, cleanroom design, and GMP consulting.
-
As the Sr Director of Operations and Program Management, I ensured FDA compliance through comprehensive regulatory analysis and worked with R&D and bioengineering teams to develop novel products and aseptic procedures. I standardized project management tools, established best practices, and mentored project managers. I built key partnerships and designed a future satellite facility in the Southeast, negotiating contracts that reduced material costs and brought the project in 40% under budget. I developed strategies for scaling manufacturing operations and authored essential QMS documentation. I also created and executed validation protocols, launched our first product, and managed growth with a $5MM CAPEX and $2MM OPEX, all while championing cGMPs and GDPs.
-
As the lead project Manager, I designed, planned, and executed the relocation of the Manufacturing department to a new 100,000+ square foot facility. I led the relocation of over 600 employees and 250 pieces of specialized equipment, ensuring seamless installation of automated systems and scheduling qualifications and validations ahead of launch. I carefully planned the relocation tasks to maintain the production schedule, ensuring that finished goods inventory and WIP were unaffected. I collaborated with engineering, operations, quality, materials management, and other departments to ensure the project's success and timely completion.
-
As the experienced Laboratory Technologist, I was responsible for training new employees, performing statistical process controls (SPCs), qualifying testing equipment, reviewing and approving diagnostic reports, and implementing Lean practices in to the lab. I also performed quantitative protein analysis via nephelometry, aiding in the diagnosis of auto-immune diseases, celiac disease, several forms of cancer, and many other diseases or illnesses.
Project successes included increasing laboratory capacity by 25%, developing workflow improvements that decreased lab turn around times by 10%, and improving reporting accuracy.
-
At Rigid Alaska, a custom manufacturer of roofing, siding, and decorative metal panels, I oversaw all manufacturing operations. I coordinated production for large-scale government projects while managing daily workflows, monitoring product quality, production KPIs, and meeting deadlines. As a startup, I established standard operating procedures, inventory practices, safety initiatives, and performed equipment qualifications and preventative maintenance
I help teams implement and integrate critical business systems
-
NetSuite | My current ERP implementation is for a pre-commercial biotech company that is converting to NetSuite Oracle from Syspro. We are also integrating financial systems with our EU subsidiary. This ERP transformation covers Procure to Pay, Design to Build, Quality, Order to Cash, NetSuite Planning and Budgeting, well as many complex integrations with other business systems.
Sage ERP | Improved financial reporting abilities for a commercial stage publicly traded life sciences company; bringing together key processes that impact financial reporting, including inventory management processes and cost accounting metrics from manufacturing and operations
-
Salesforce | I have helped drive early commercial design, development, and implementation of a full service CRM using the Salesfore platorm. Our processes included customer service, order management, improved customer experience, customer lifecycle management, and more.
-
Compliance Quest | This project covered designing, configuring, and launching an eQMS that was built on SalesForce. We migrated all processes and data from the historical QMS.
EtQ | Industry leading eQMS. Managed multiple module implementations, including Document Control and Training.
MasterControl | Managed the QMS implementation and migration from a fully paper QMS to our full document control and training system within MasterControl.
-
Q-Bench | Led the design, implementation, and validation of the LIMS for a CLIA approved diagnostics company. System included patient and provider portals, automated data connection with laboratory equipment, QC records, and batch record creation.
BSI Systems | Led the design and implementation phases of the LIMS for a commercial and publicly traded biotech company.
-
Planon | I led the team and implementation of the Planon system. This involved scoping the system, gathering business requirements, selecting an implementation partner, and overseeing the implementation.
-
Revenue Cycle Management
Manufacturing Resource Planning
Procure to Pay Tools
Warehouse Management Software
Fixed Asset Management System
Equipment Tracking and PM
I also like to build things
I have helped teams design, build, and validate industry leading cGMP manufacturing facilities, modular ISO 7 cleanrooms, and controlled production environments.
I have led capex projects with values greater than $50M, built over 20,000 square feet of ISO 7 cleanroom environments, and directly managed over 150,000 sq ft of manufacturing space.
Professional References
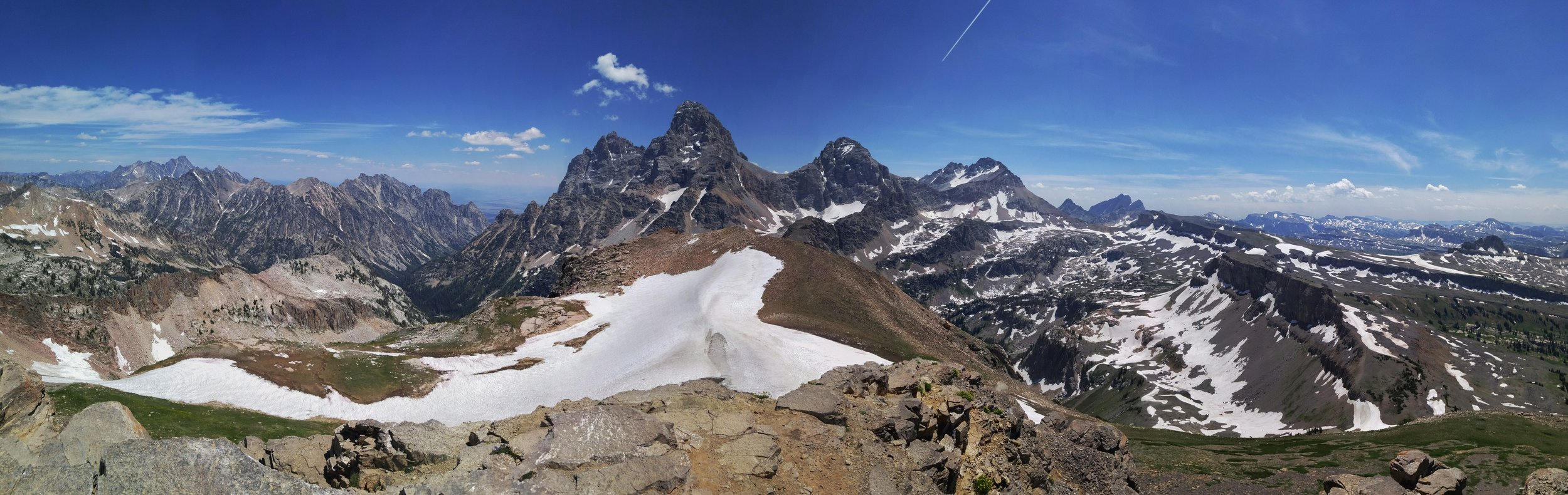
Biking | Fishing | Family | Outdoors | Hobbies |
Biking | Fishing | Family | Outdoors | Hobbies |
Father of three boys - avid angler - mountain bike enthusiast - novice photographer
I have been fortunate to live in and explore some of the most beautiful areas in the US. From mountain tops to desert canyons, here are some pics of my favorite places.
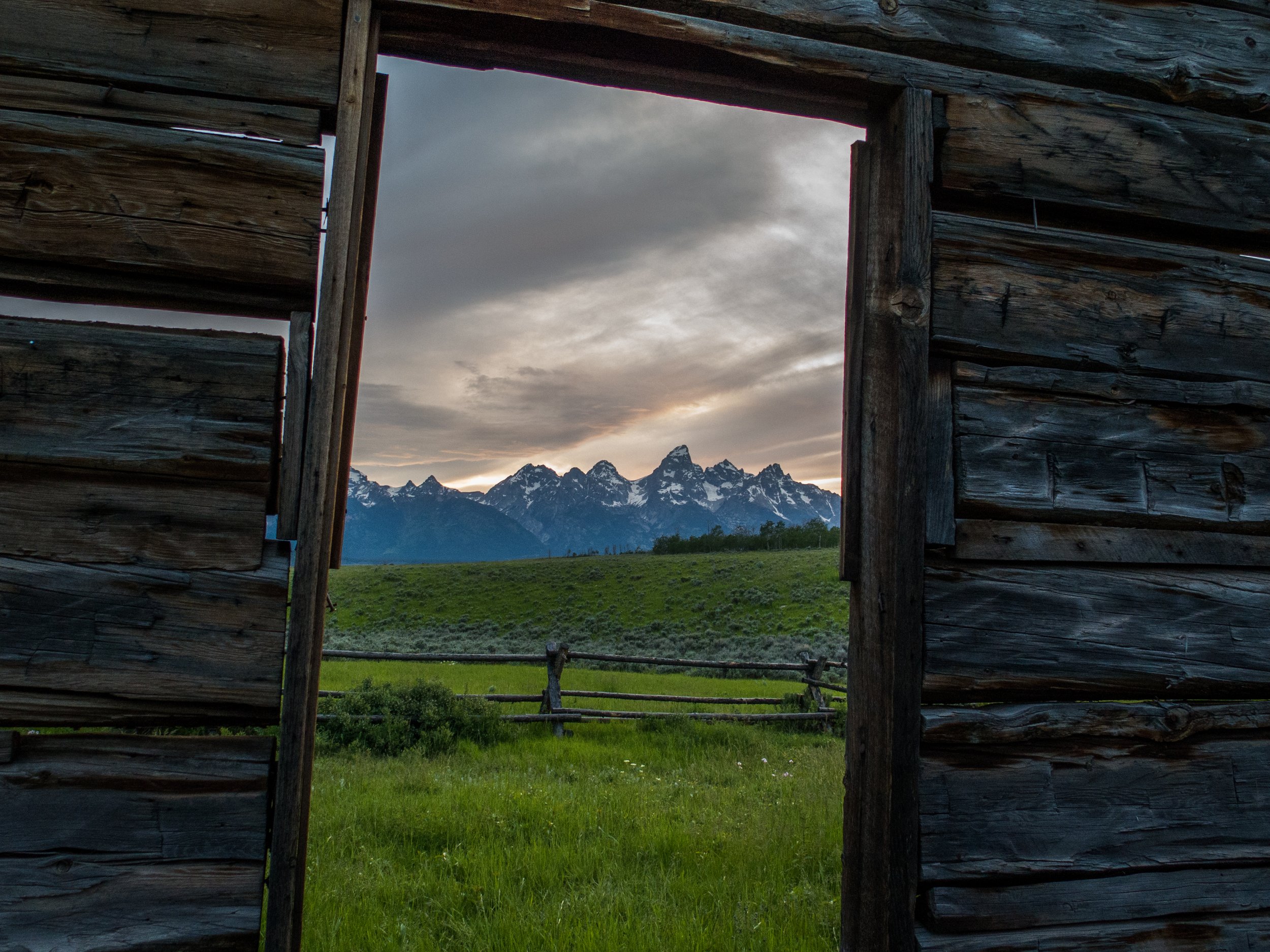
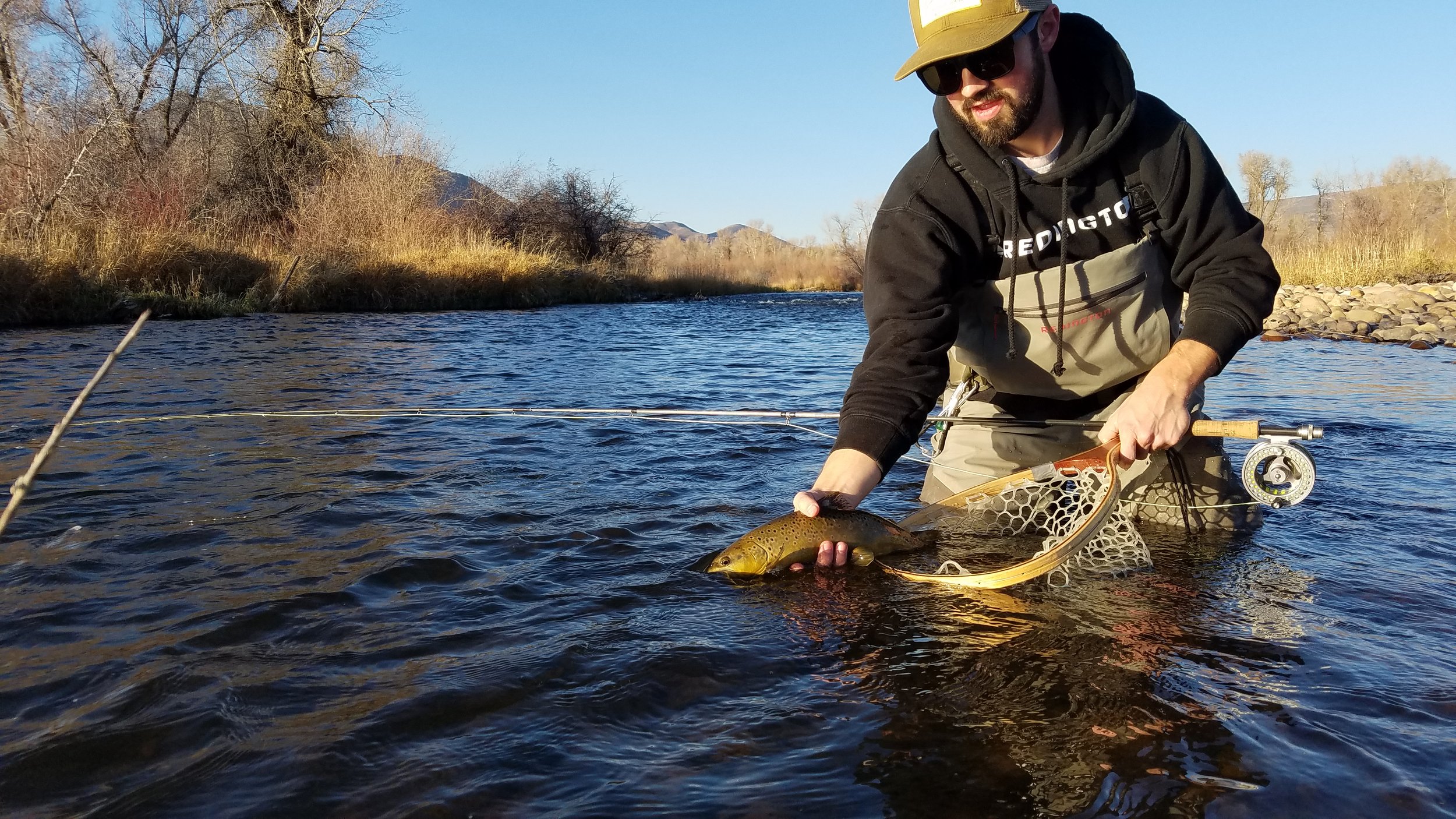


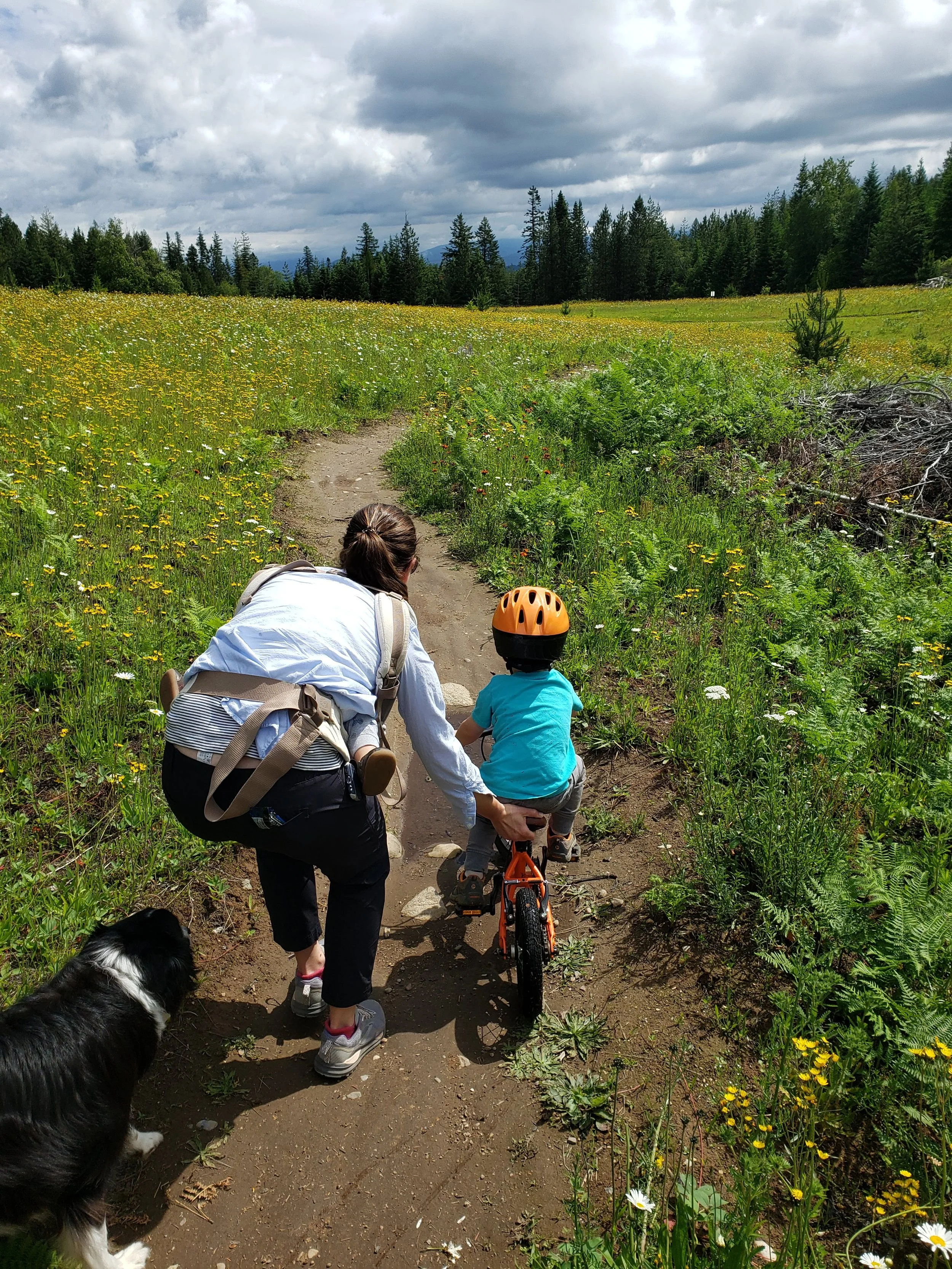
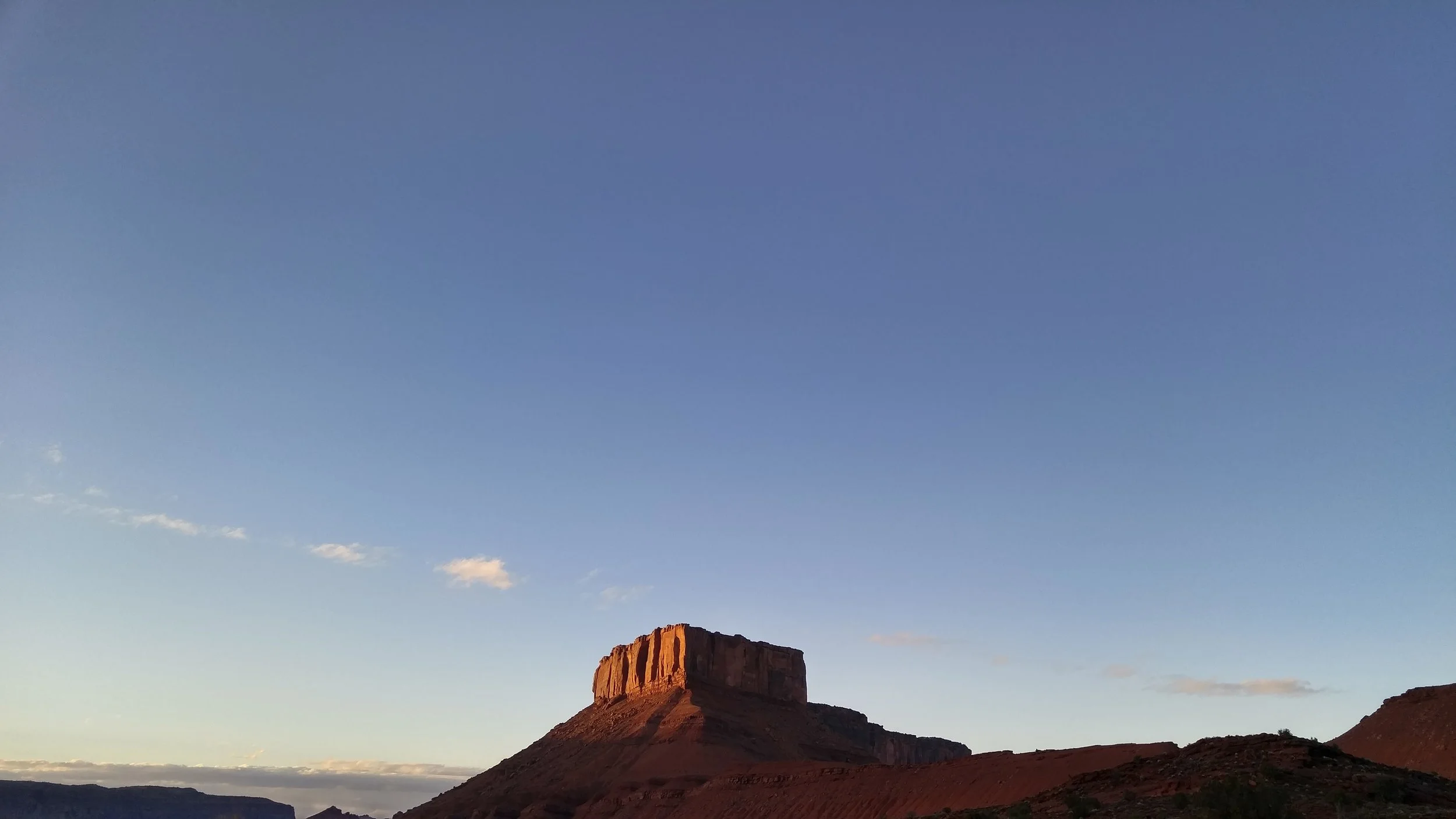
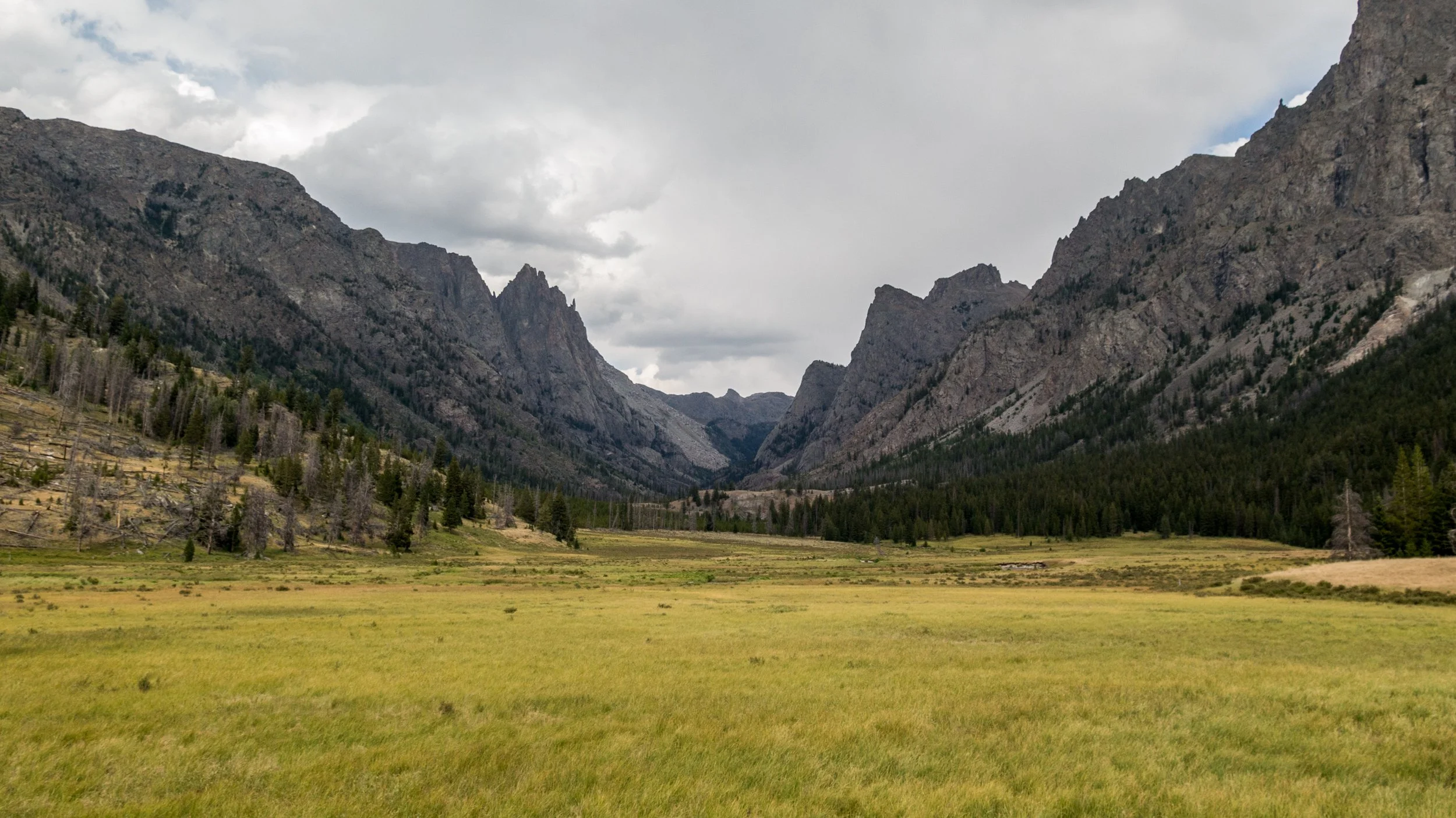






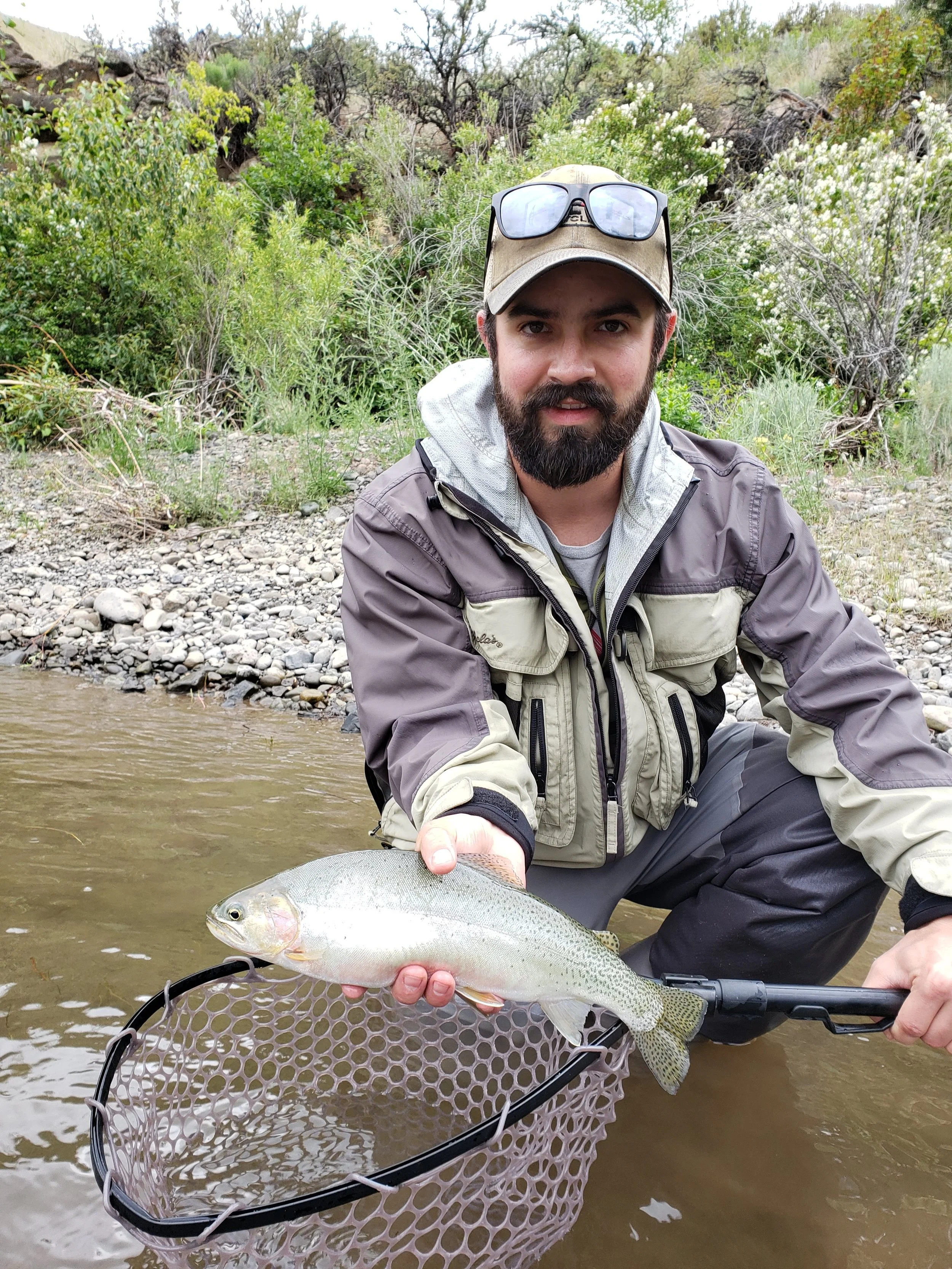
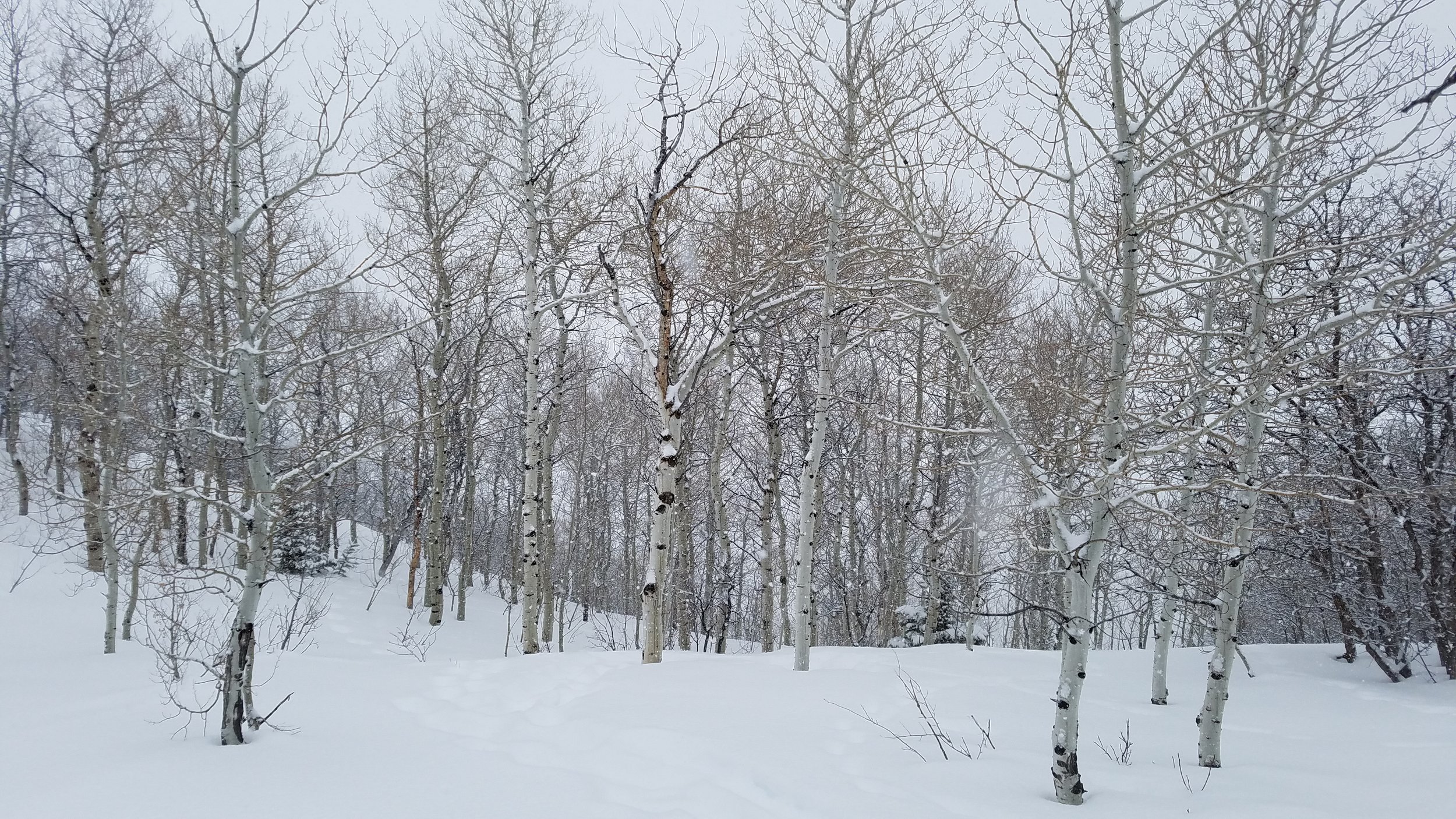
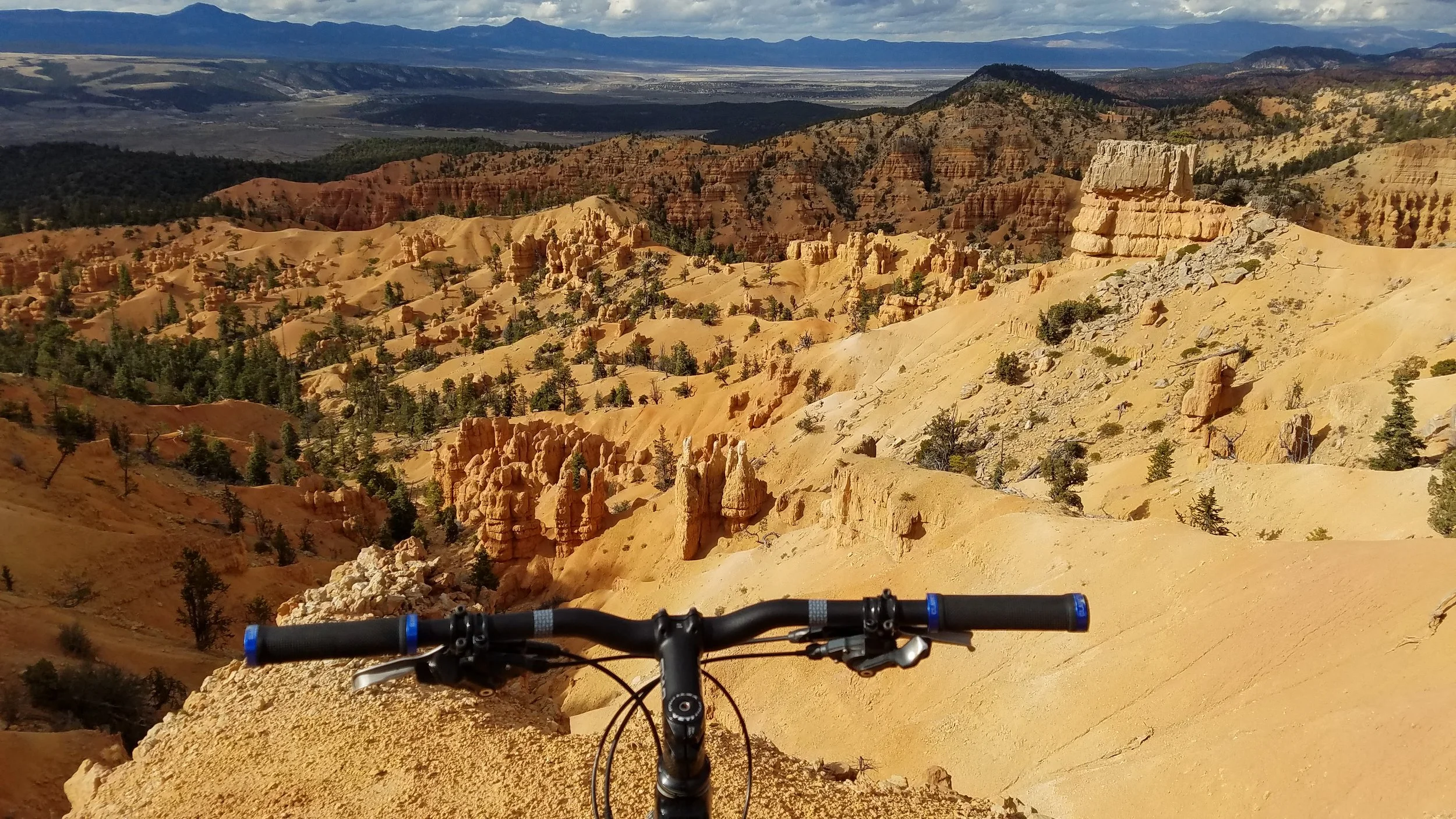

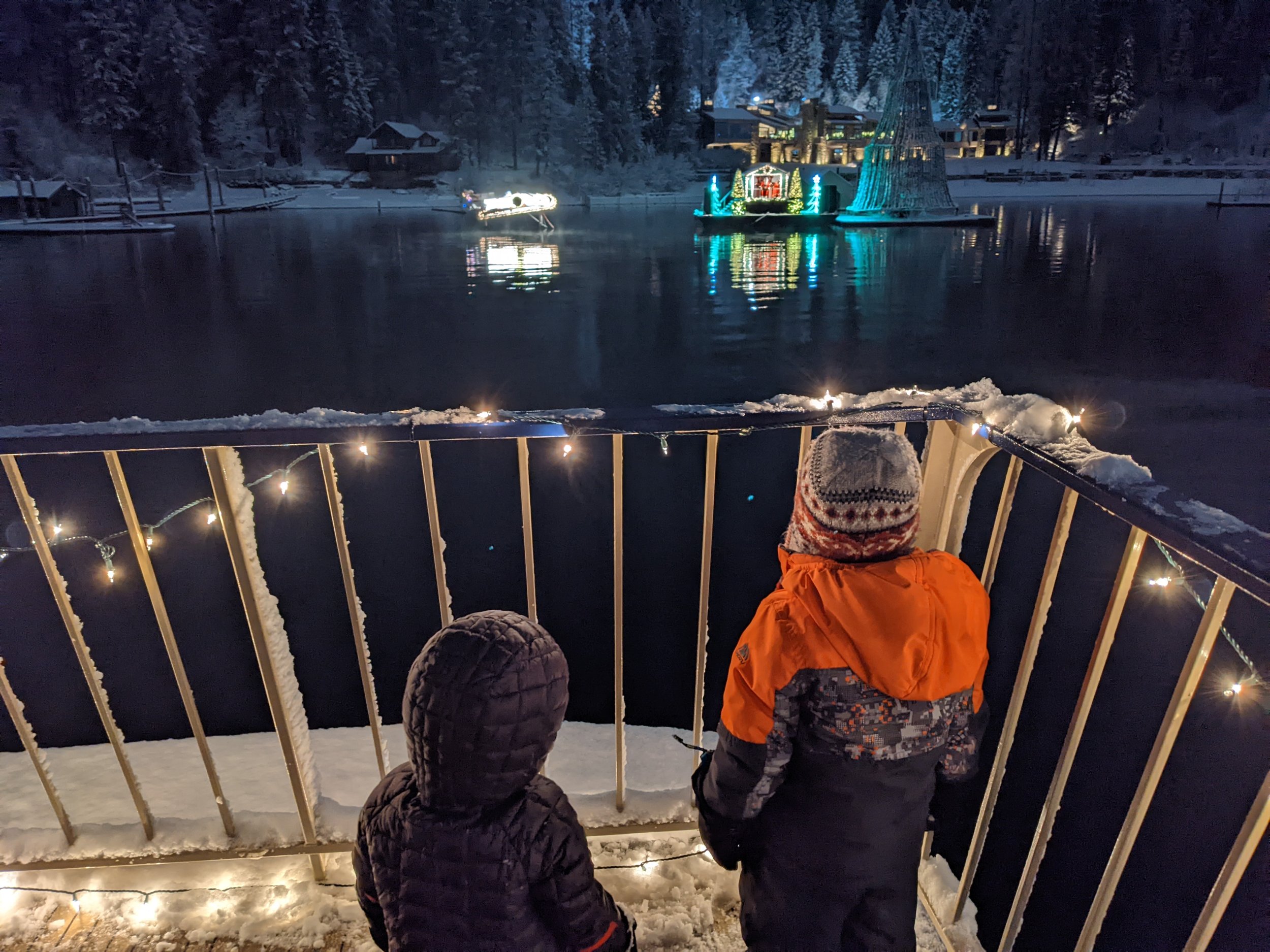
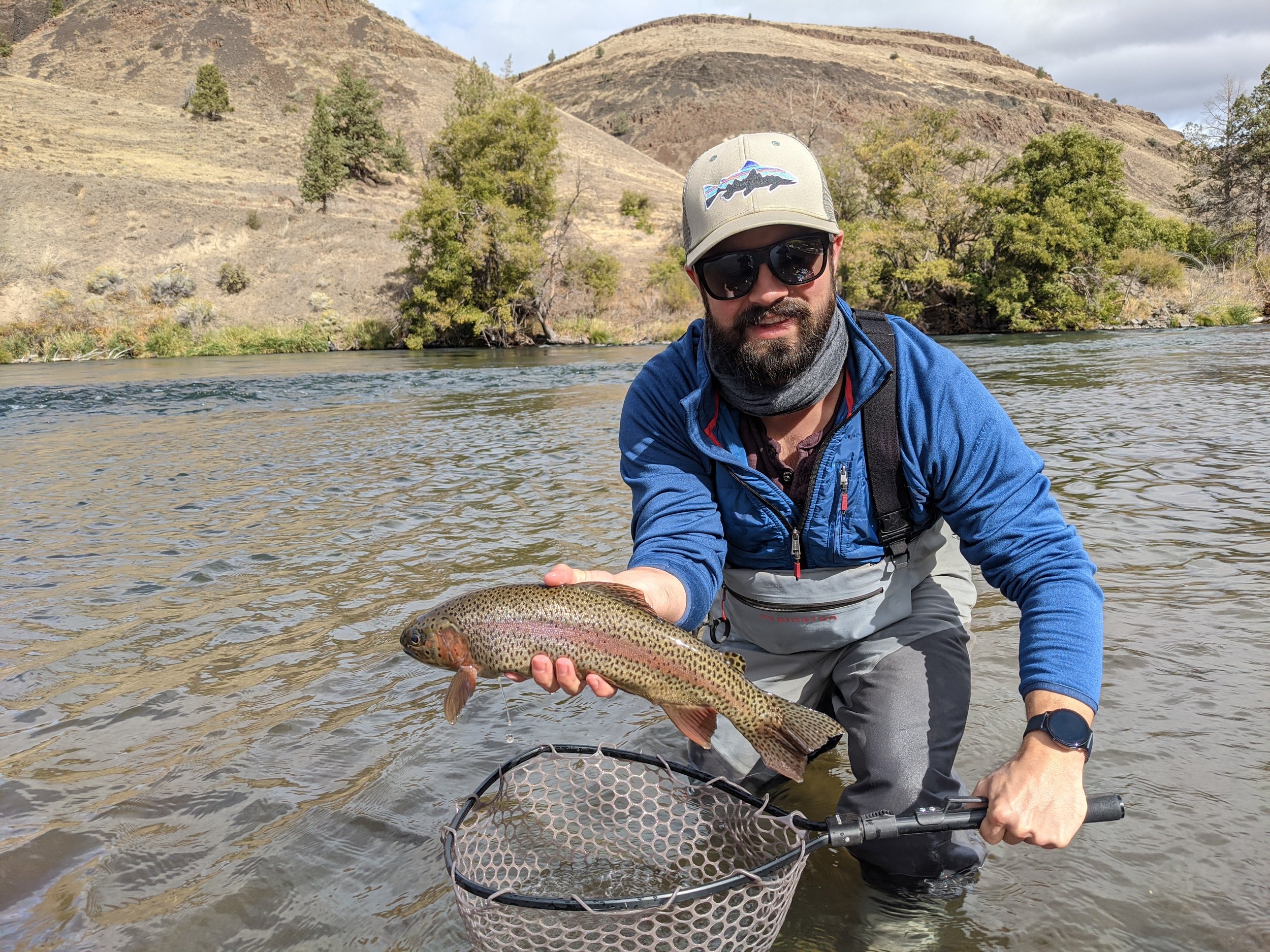
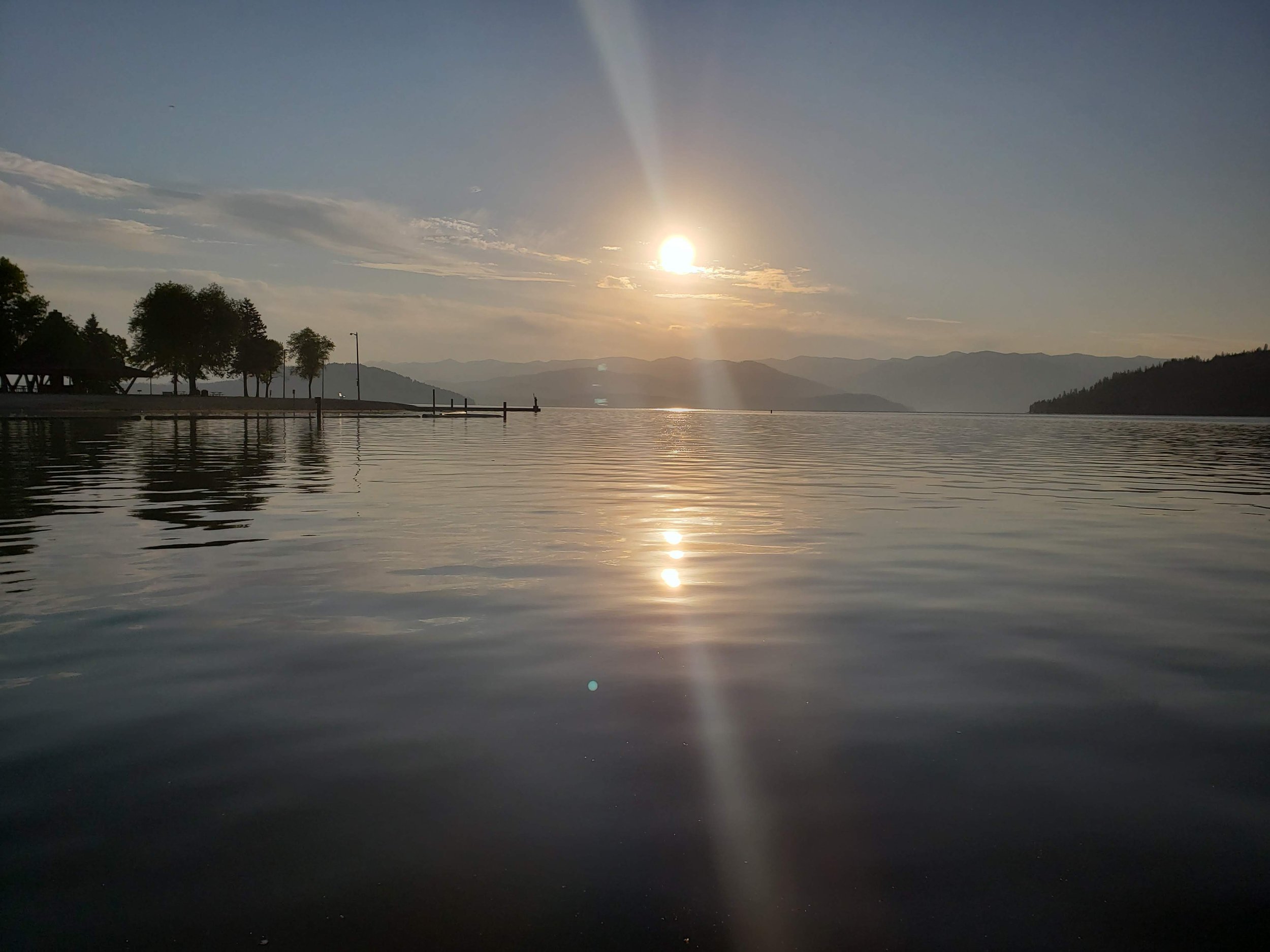
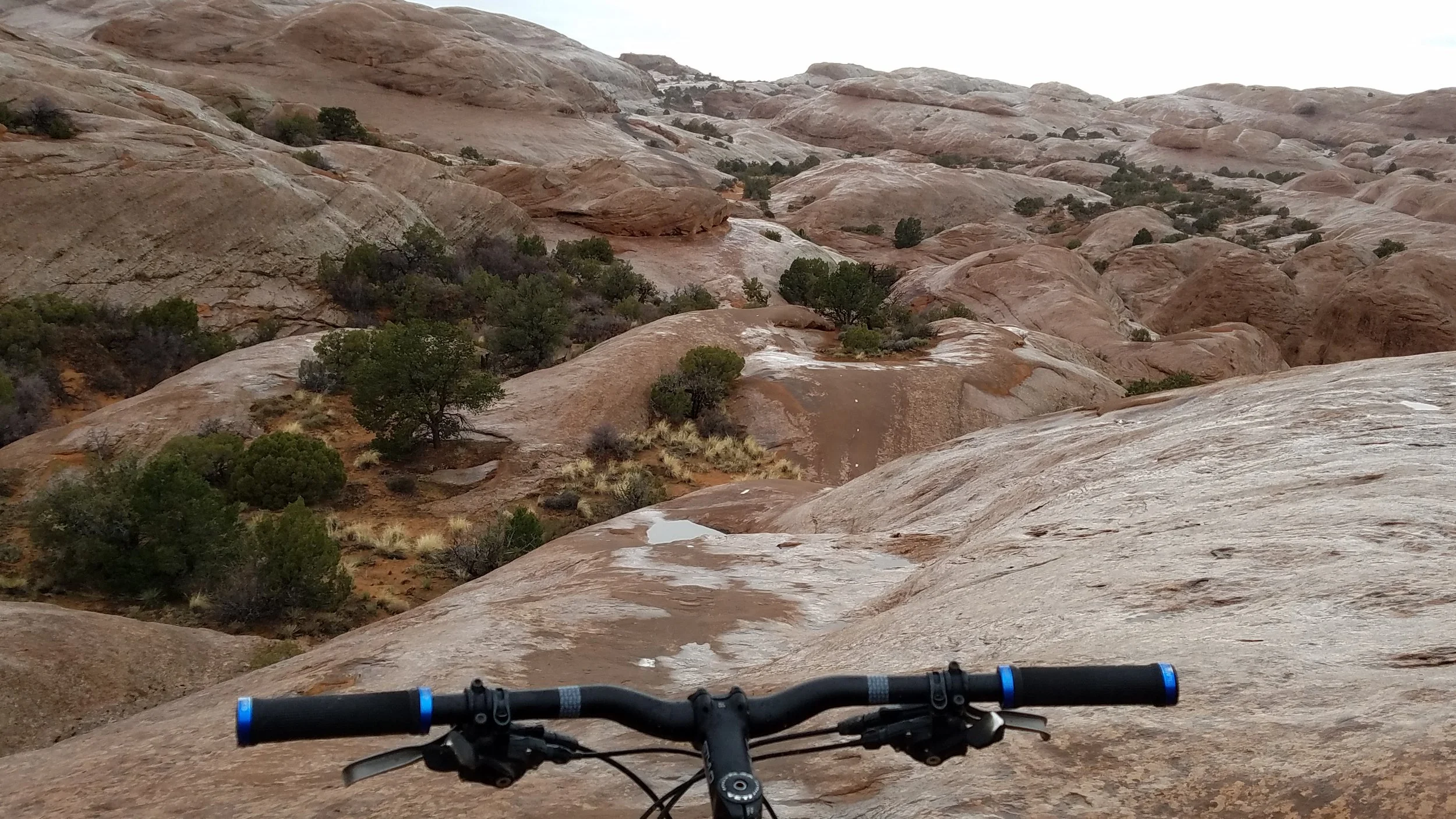
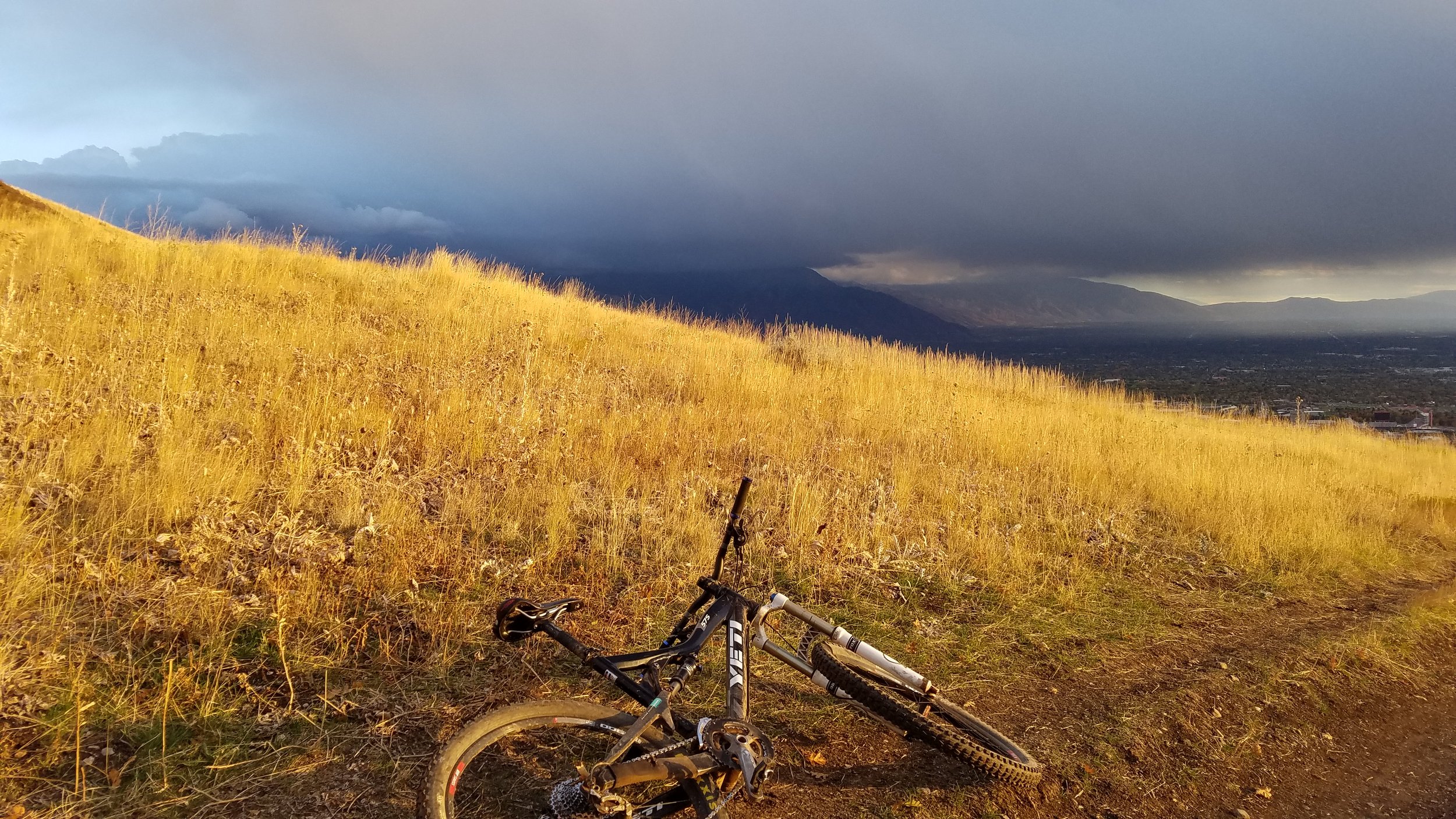
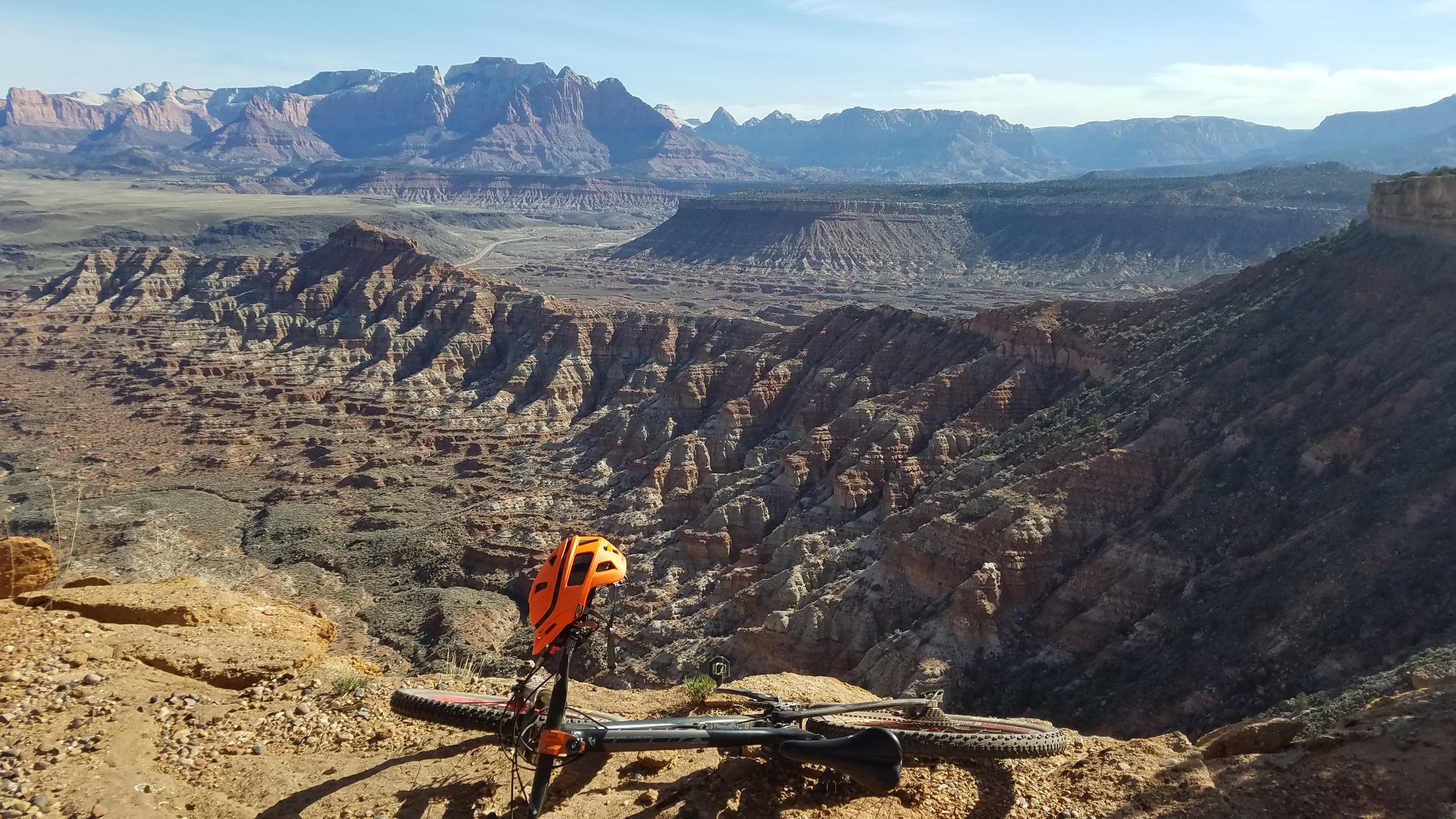

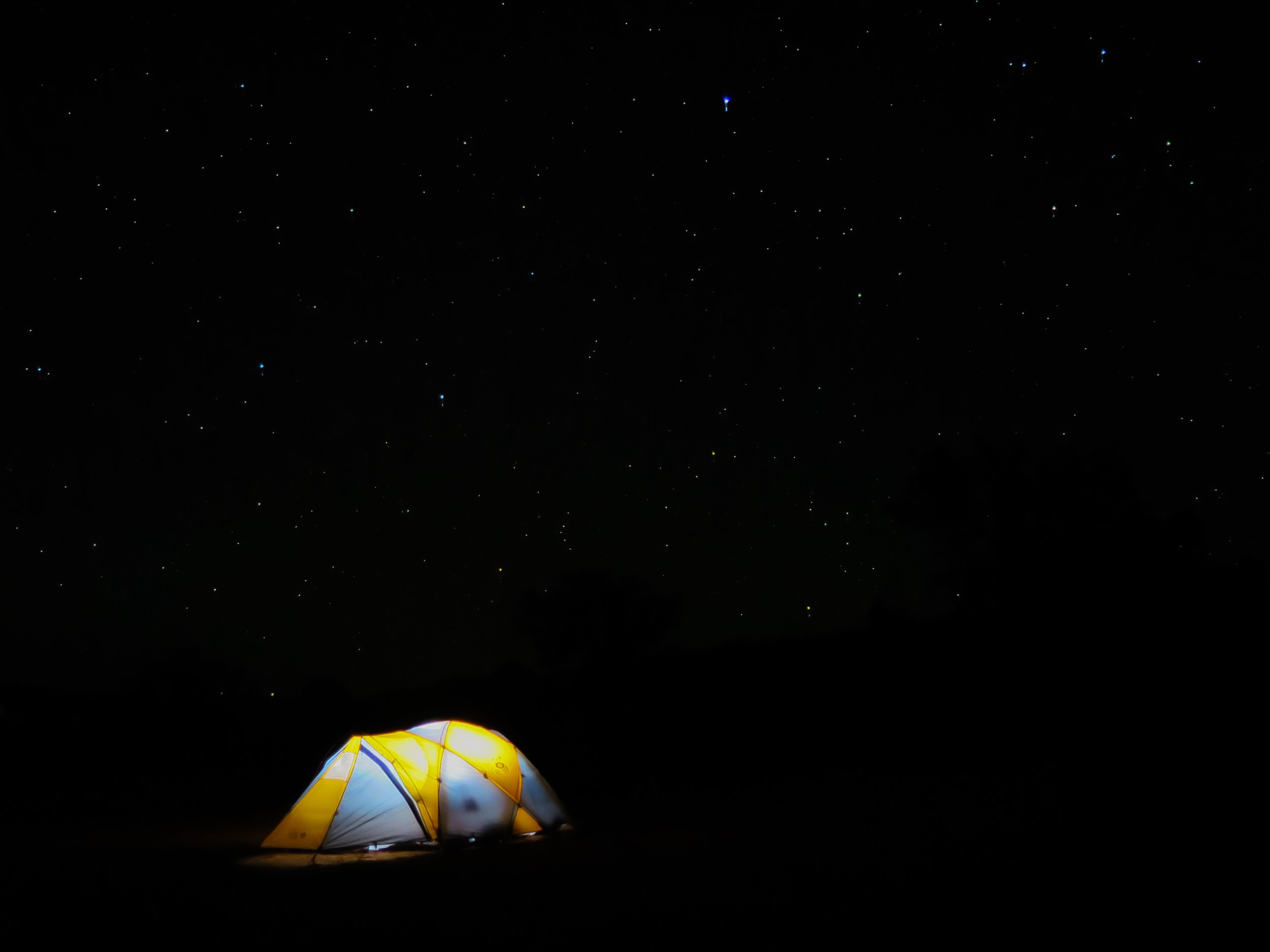
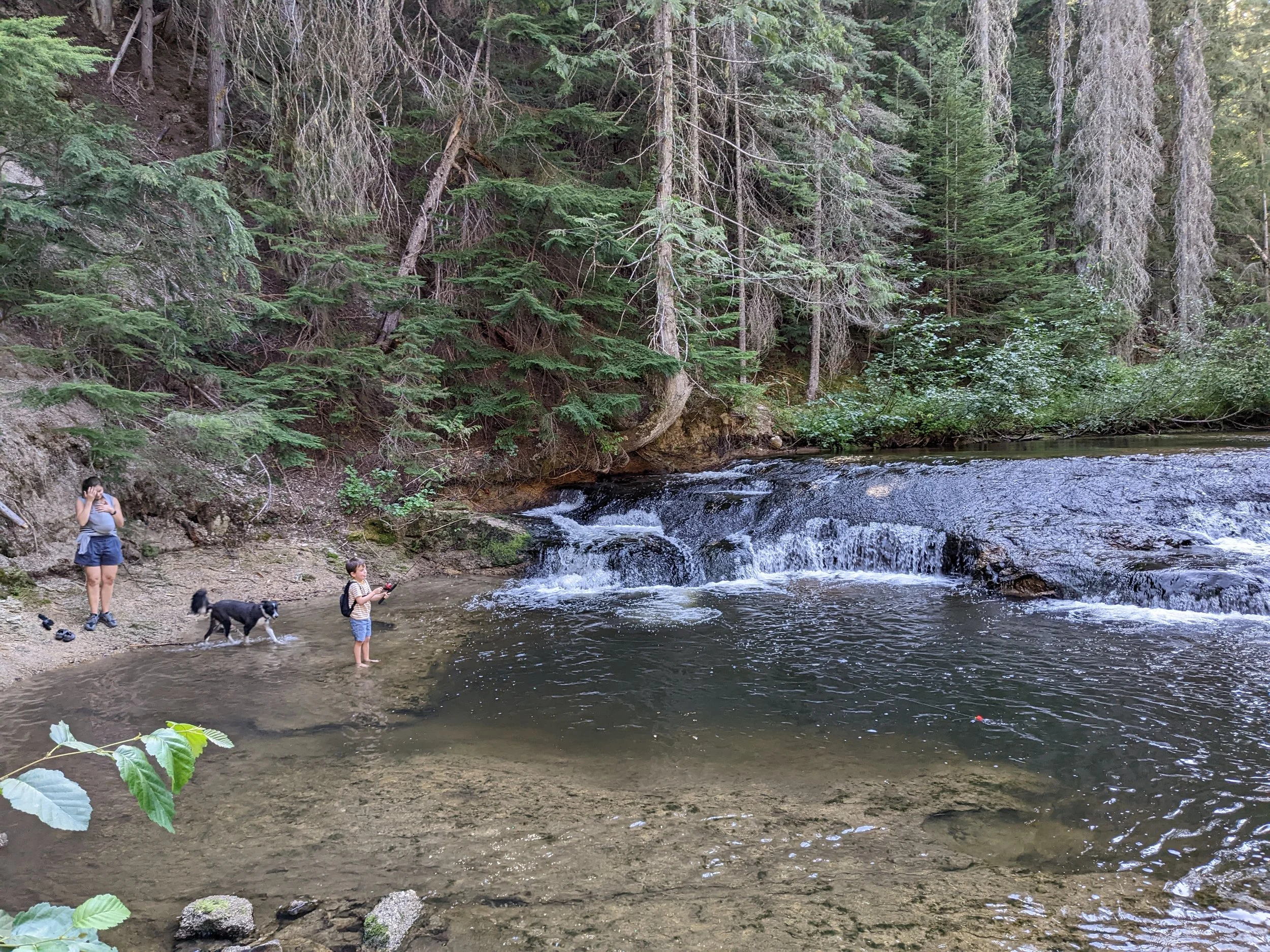
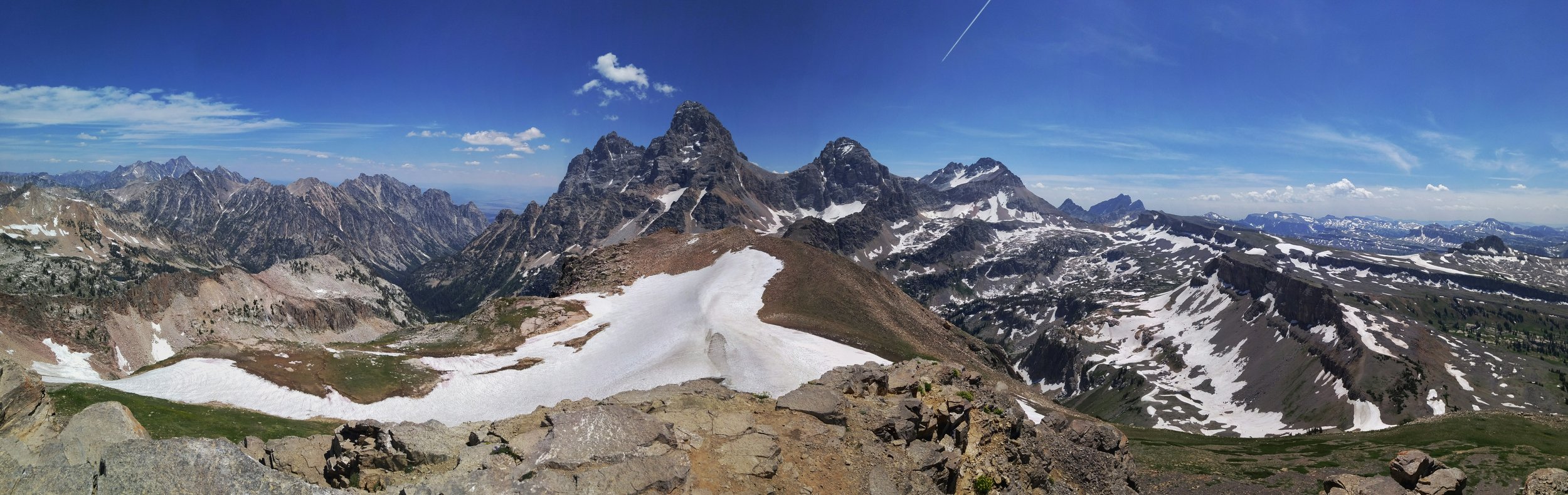

